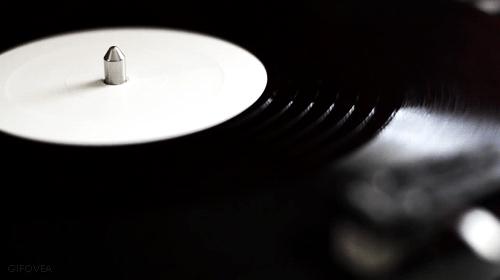
How an LP record is manufactured
1). The two-track final mixed master tape is delivered from the recording studio to a 'cutting centre' and is started up. An electronic stereo signal from the playback machine heads is transmitted to the cutting head attached to a record turntable lathe (see below). This heated cutting needle oscillates as it cuts in to the plastic surface of the acetate on the lathe which revolves at exactly the appropriate speed. An acetate is a perfectly flat circular sheet of aluminium, coated on both sides with a thin layer of vinyl. As the long continuous groove is cut into the vinyl making its way slowly towards the centre, its waste is extracted by a vacuum pump. When that side of the disc is full, a matrix number is inscribed between the run out grooves of the newly-cut acetate to identify which disc it is; this would normally be the catalogue number allocated to that item and would be inscribed by hand or imprinted by a machine. Every record company's pressing plant have their own coding but on Philips group discs, a suffix would be added at the end of the catalogue/matrix number with either '420' if the master was cut in the UK, or '670' if it was cut in Baarn, Holland - as most classical items were. The last codes to be added to the matrix would identify which side of the disc it was ( /1 or /2) and whether it was a mono recording (L), or stereo (Y).

an acetate
2). A metal ‘stamper’
is then created from this by means of electrolysis/electro-forming, for each side. An electric current is passed between the acetate and a layer of silver nitrate solution is coated on it. The nitrate fills all of the grooves in the lacquer master. Then the disc is submerged into a nickel sulphate electrolyte solution and allows nickel to deposit through a chemical process onto the disc plate. This takes about an hour and a half and when it’s done it is carefully separated and a perfectly formed metal negative from the lacquer has been produced - the master stamper. This is of course an impression, so that the grooves are actually sticking upwards. These will later literally 'stamp out' the vinyl disc - hence the name given.

a cutting lathe

LP stamper

45 stamper

3). Placing side one and side two of the album’s (or a single’s) stampers onto the jaws of a record press and then positioning the record labels in the middle and against the stampers. Placing a measured amount of black plastic (vinyl) pellets on the bottom label.
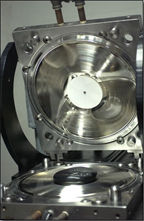
plastic pellets
record press
4). Then the record press jaws are closed (not unlike a sandwich toaster!) and with water circulating at 400 degrees Centigrade in tubes under hydraulic pressure, the heat then melts and secretes the vinyl over the entire stamper surface.

5). After a short while cold water is then pumped through the tubes reducing the temperature, enabling the vinyl to set firm.
6). Then after a few seconds more, by lifting the hydraulic jaws of the press, a perfect impression of the album is completed.
7). Any overspill of the vinyl plastic is then trimmed off on a circular lathe and the album inspected before being placed in its polythene bag
8). Records are then checked by quality control every 70 or 100 copies and finally placed in its outer record sleeve by staff in what is known as a 'finishing shop'.
Any imperfect LPs rejected by quality control are then withdrawn, the label is punched out - making the LP appear like a giant black Polo mint - before the plastic is crunched up, re-cycled to be used in the manufacture of 45s.
excess plastic being trimmed off the edge
9). On new releases the labels may not yet have been printed, so the first pressings are known as ‘white labels’ and sent to A&R chiefs for approval. It is checked here again to ensure it is the correct album and the tracks are in the correct order. The details for the printed label may take some time to complete as each song/track has to be approved by the appropriate music publisher. The particular example below is of the very first Fontana LP released in the UK in 1958.

a White Label pressing
So, do Vinyl Albums sound better than Compact Discs?
Much has been written and passionately discussed concerning audiophiles' preference over the playback quality of the sound reproduction of CDs against vinyl LPs.
In the end of course, it is a matter of personal choice of the listener. Generally speaking, a CD is difficult to damage and is obviously more compact for storage. But it is well worth reading what Telarc Records audio engineer Bob Woods* had to say about the virtues of each format: "We learned one very clear thing about LPs. All you have to do is to take a blank lacquer, have no signal coming down, cut a series of silent grooves, put it on to a turntable - and what do you get on playback? You get a soft hissing sound - a nice, soft, round 'pink noise'. Everything you're listening to on an LP is being heard through that filter of pink noise. And so it has the tendency to feather the edges of things. It gives the record a sense of a little warmth. Violins sound like really special violins. But if you stand in front of a real violin, it's got some grit. It's got an edge to it". In other words the LP conveys a softer sound to the human ear which in turn, makes it appear warmer and not such cutting edge technology. Whatever you think of the effect that aggressive rampant dynamic-range compression has had on music, the fact remains that these compressed recordings, technologically speaking, are a step backwards. The typical dynamic range of a contemporary CD is smaller than that of the recordings made in the pre-digital era.
4.8 million vinyl records were sold in the UK alone in 2020, a 10% increase from the previous year and the highest number in 30 years.
http://electronics.howstuffworks.com/question487.htm
*Taken from 'Perfecting Sound Forever - the Story of Recorded Music' by Greg Milner